-
Choose your category:
-
- Exploration Solutions
- Core & Well log analysis
- Geochemical Analysis and Interpretation
- Petrophysical Interpretation
- Rock Physics, Seismic QI
- Geomechanics
- Basin Analysis and Regional Studies
- Geological interpretation and Modeling
- Prospect Inventory and Risk analysis
- Drilling & Completion
- Concept Selection, Conceptual Design
- Preliminary well design and planning
- Detailed well design and planning
- Integrated Reservoir Study
- Core & Well log analysis
- Petrophysical Interpretation
- Rock Physics, Seismic QI
- Geomechanics
- Geological interpretation and Modeling
- Static Modeling
- Basic Reservoir Engineering
- Dynamic Modeling
- Uncertainty Analysis and History Matching
- Production Forecasting
- 4D Seismic
- Increased Oil Recovery
- Fast increase oil recovery Solutions
- EOR; from concept to field implementation
- Economic Studies & Risk Evaluation
- Production Engineering
- Flow Assurance
- Artificial Lift Design
- Material Selection
- Production Chemistry
- Surface Facilities
- Flow Assurance
- Process and facility engineering
- Material Selection
- Operation Assurance
- Production Chemistry
- OTS & Dynamic Simulation
Material selection
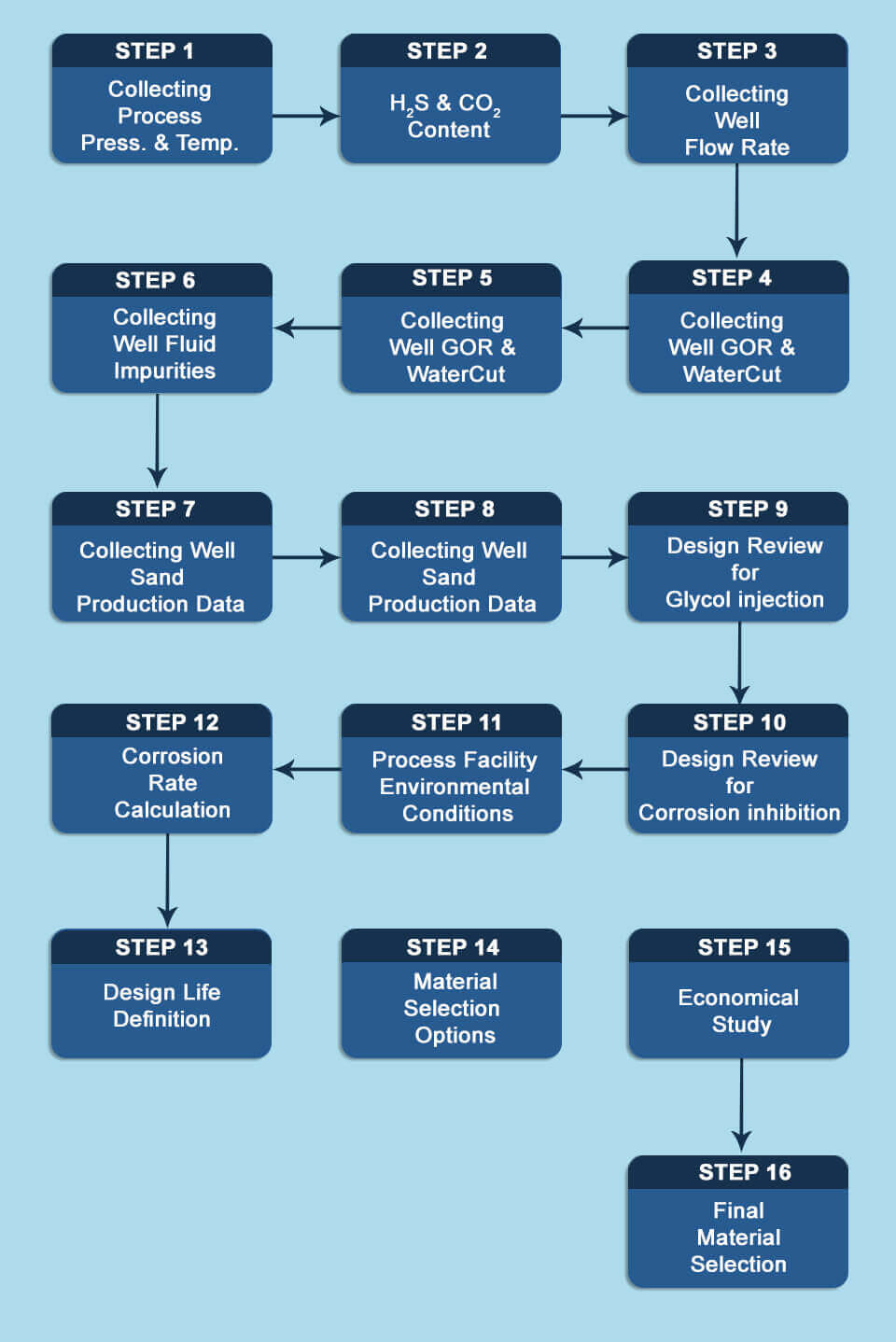
In order to have sustainable and reliable production, selecting the proper material is a critical step in the design process. Selection is further refined by cost considerations in which capital expenditures (CAPEX) and operational expenditures (OPEX) are balanced to minimize total lifetime cost. Since the exploration of deeper oil and gas reservoirs continue to grow, material selection and testing become more and more crucial for engineering and operating companies. In addition to higher pressure and higher temperature reservoir fluids, increasing CO2 and H2S contents, make the need for higher grade corrosion resistance alloys inevitable. In some cases having impurities like high chloride salts along with elemental sulfur, make the design of down-hole and surface facilities more complex.
At NAED we combine the knowledge and experience obtained from years of experiences of our people and partners with the requirements of the clients in order provide the most optimized integrated design and testing services.
While materials can be selected based on the process described, fitness for service testing is an acceptable method to prove a material can work in a given environment and is required if no data is available to confirm the alloy is acceptable. Having firm agreements with our partners’ laboratories provides the opportunity to our clients to have immediate access to the following test facilities:
Specific Corrosion Rate Testing
Sour Service Compliance Tests
NACE TM 0177 Sulphide Stress Cracking and Stress Corrosion Cracking in H2S Environments Tests
NACE TM 0198 Slow Strain Rate Test
EFC 17 Elemental Sulphur Corrosion Testing